Letting Apple off the hook for labour abuses
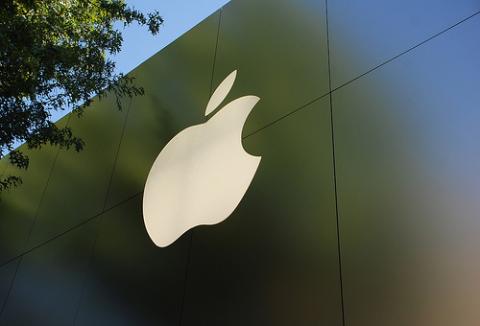
As long as labour abuses remain in far-off places rarely subject to scrutiny by the likes of the New York Times, companies like Apple will remain more swayed by stockholders pushing to maximise their profits than consumers who want the workers who make their iPods and iPads treated justly. By Julie Hollard.
“The iEconomy,” a New York Times series “examining challenges posed by increasingly globalized high-tech industries,” provides Exhibit A on how even the best attempts by corporate media to dig into international labour rights fall short.
With three bylined reporters and nine months of work (Economix,1/25/12), the first two pieces of the series provided perhaps the most in-depth look at the production of Apple products that a corporate outlet has ever published. Despite all the resources it had expended and the abuses it had documented, the Times refused to pin the responsibility on Apple.
The first article (1/22/12), “How the U.S. Lost Out on iPhone Work,” made the case that globalization has essentially forced Apple to make its products almost entirely overseas. Largely sourced to anonymous current or former Apple employees, the piece gave an insider look at the supply chain and decisions about outsourcing that emphasized it’s not just about costs and profit:
It isn’t just that workers are cheaper abroad. Rather, Apple’s executives believe the vast scale of overseas factories as well as the flexibility, diligence and industrial skills of foreign workers have so outpaced their American counterparts that “Made in the U.S.A.” is no longer a viable option for most Apple products.
Note the word “flexibility,” a word repeated multiple times in the article. What flexibility means in this context is being able to hire and fire thousands of people at once, which, since companies don’t have to keep paying workers during slow times or provide severance, makes labour cheaper—exactly what the Times said isn’t going on here. It also means a lack of workplace regulations and enforcement, such that when Apple needs something fast, the factory foreman can drag thousands of employees out of their beds in company dorms to get back on the line—a story told to the Times by an anonymous former Apple executive, who proudly describes that “speed and flexibility” as “breathtaking.”
The second article (1/26/12), “In China, the Human Costs That Are Built Into an iPad,” compiled a damning list of those “human costs” of the Apple supply chain in China: child labour, excessive overtime, wage withholding, hazardous work conditions leading to death and injury, and a string of worker suicides. Notably, the piece quoted critics who cited Apple’s emphasis on profits that squeeze suppliers, its lack of transparency and its failure to rigorously enforce its own standards.
But witness the piece’s conclusion:
People like Ms. [Heather] White of Harvard [and a former member of the Monitoring International Labour Stand-ards committee at the National Academy of Sciences] say that until consumers demand better conditions in overseas factories—as they did for companies like Nike and Gap, which today have overhauled conditions among suppliers—or regulators act, there is little impetus for radical change. Some Apple insiders agree.
“You can either manufacture in comfortable, worker-friendly factories, or you can reinvent the product every year, and make it better and faster and cheaper, which requires factories that seem harsh by American standards,” said a current Apple executive.
“And right now, customers care more about a new iPhone than working conditions in China.”
In other words, both pieces conclude that none of this is really Apple’s fault. And what’s more, all would be well if consumers would just push Apple to change—like they did Nike and Gap—instead of going gaga over each new release of an Apple product.
Times reporter Keith Bradsher repeated that message to New York public radio’s Brian Lehrer (WNYC,1/27/12): “The working conditions are not what Americans would accept at all. And yet Americans implicitly accept them by buying the products they produce.”
It’s a curious accusation. How can people accept—implicitly or explicitly—labour abuses that they’re scarcely even aware of? In the year preceding publication of the first “iEconomy” piece, the Times published 385 articles about Apple. In that coverage, you’ll find the word “genius” more often (19 times) than you’ll find the word “labour” (12). And of those pieces that do mention labour, only nine—2 percent of all articles about Apple—are actually about labour abuses. Just the week before, the Times had published a “factcheck” about Apple outsourcing that put the blame squarely on a lack of educated Americans. (See sidebar.)
Meanwhile, many articles quite directly push Apple products on readers: One Times reporter (12/7/11) admonished that one is “never fully dressed without a smartphone. In 2011, a smartphone is no longer a newfangled doodad—it’s table stakes for the modern world. There are iPhone 4s for $99 now, and iPhone 3GSs are free with a contract, so there really are no excuses.” An earlier review (10/12/11) was headlined “New iPhone Conceals Sheer Magic.”
Who is it, again, that’s implicitly accepting the working conditions for people who make our Apple products?
The problem becomes even more evident when you add the uncomfortable fact that Nike and Gap are not paragons of labour rights abroad, as the Times would have readers believe—and would be forced to acknowledge if it actually kept up its reporting on such things.
Just over a year ago, a fire in an apparel factory in Bangladesh killed at least 27 workers and injured around 100. Some jumped to their deaths from the tenth floor, tragically reminiscent of the Triangle Shirtwaist Factory fire in New York 100 years earlier that helped drive forward the movement for collective bargaining and workers’ rights in this country. The Times (12/14/10) noted the incident, but didn’t report who the factory was producing clothing for. It was Gap (Guardian, 12/14/10).
As for Nike, high-profile activism, largely student-led, forced Nike to make public gestures toward labour rights more than a decade ago—the company helped form the Fair Labour Association, a corporate-supported monitoring group that allows companies like Nike to claim their products are sweatshop-free. This same group is now making Apple its first technology company member.
Yet Nike factories continue to be plagued by labour abuses. In 2009, two Nike factories in Honduras abruptly closed and laid off 1,700 employees after workers started organizing unions. The laid-off workers were not paid the severance or health benefits they were legally owed; they also complained of having regularly worked unpaid overtime (Labour Notes, 4/29/10). After a long student-led campaign that eventually resulted in several universities boycotting the company, Nike agreed to pay the severance.
So, “radical change”? Not exactly. And the pressure on Nike and Gap has been remarkably strong and well-organized, by groups like United Students Against Sweatshops and the Institute for Global Labour and Human Rights.
As long as labour abuses remain in far-off places rarely subject to scrutiny by the likes of the New York Times, Nike, Gap and Apple—and all the other multinational corporations whose names could easily substitute for them—will remain more swayed by stockholders pushing for maximized profits than consumers who want the workers who make their shoes, clothes and iPods treated justly. {jathumbnailoff}
Originally published on FAIR under a Creative Commons by-nc-nd license.
Image top: afagen.